Mit dem Laser Platinen herstellen: der Laser4DIY
In der ersten Runde des Prototype Fund Hardware werden sechs Projekte gefördert. In dieser Interviewserie stellen wir sie vor. Mit Andreas Kahler und dem Projekt Laser4DIY machen wir den Anfang. Andreas Kahler ist Mitgründer und Vorstand des FabLab München e.V. Er beschäftigt sich dort mit der Entwicklung von Open-Hardware-Geräten, wie dem Laser4DIY. Dafür arbeitet er mit Andreas Welzmüller (Laserexperte und verantwortlich für das Design der Laserquelle) und Tobias Gutmann (Physiker, zuständig für Elektronik) zusammen.
Andreas, an was arbeitet ihr genau?
Wir bauen ein Gerät, das mithilfe eines Lasers Elektronikplatinen herstellen kann. Platinen sind die Grundlage von allen elektronischen Geräten, auf ihnen sind die Bauteile miteinander verbunden, durch sogenannte Leiterbahnen. Die brennt unser Laser in eine Kupferfläche, nach dem Vorbild eines digitalen Designs. Man spricht dabei auch von “Laserstukurierung”.
Für die Herstellung von Platinen gibt es verschiedene Möglichkeiten. Bei dem Laser handelt sich um eine elegante Methode, weil es berührungsfrei funktioniert und sich damit sehr feine Details abbilden lassen. Etablierte Methoden, wie das Isolationsfräsen oder Ätzen funktionieren anders und haben Nachteile. Beim Ätzen muss man mit gefährlichen Chemikalien hantieren und man produziert Sondermüll. Beim Isolationsfräsen handelt es sich um ein ähnliches Verfahren wie bei der Laserstukurierung. Statt einem Laser wird dort mit einer Fräse das Kupfermaterial abgetragen. Der Nachteil dieser Methode ist die erreichbare Auflösung, denn die Fräsbahn kann eine gewisse Breite nur schwer unterschreiten. Mit dem Laser lassen sich beide Nachteile überwinden, da keine ätzenden Chemikalien zum Einsatz kommen und sich sehr hochauflösend arbeiten lässt.
Das klingt nach einem super Verfahren! Welche Vision verfolgt ihr damit, für wen baut ihr euer Gerät?
Ich habe das FabLab in München mitbegründet und komme aus dem Umfeld der Offenen Werkstätten. An solchen Orten versuchen wir anderen Werkzeuge, Maschinen und Methoden zur Verfügung zu stellen, um möglichst viele Dinge selbst machen zu können. Natürlich können wir auch Services nutzen, um beispielsweise Platinen herstellen zu lassen. Allerdings gibt es dabei zwei Probleme: Zum einen möchten unsere Nutzenden mit den Maschinen experimentieren und das Verfahren sozusagen in den eigenen Händen halten. Auch, um Dinge machen zu können, die nicht zum Standard eines Dienstleisters gehören. Zum anderen dauert es einfach länger, etwas in Auftrag zu geben, als es lokal schnell selbst zu fertigen. Vorausgesetzt, es gibt eine geeignete Maschine dafür. Es in Auftrag zu geben führt zu Verzögerungen in einem Projekt. Das passt nicht zum “Rapid Prototyping” und kurzen Iterationszyklen. Durch das schnelle Testen werden Fehler sofort erkannt und der kreative Prozess bleibt lebendig.
Das sind wichtige Anwendungsfelder. Ihr werdet sicher häufig gefragt, wieso ihr euer Design als Open Source zur Verfügung stellt, was antwortet ihr?
Generell sind wir Open Source Fans. Das kommt daher, dass wir aus dem FabLab-Umfeld kommen. Ohne Open Source bzw. Open Hardware könnte unser Ort, wie er heute ist, wahrscheinlich nicht existieren. Zahlreiche Maschinen sind bei uns offen. Einerseits, weil sie oft sehr viel günstiger sind. Andererseits können wir sie selbst reparieren, warten und mit ihnen experimentieren, um sie z.B. an unsere Bedarfe anzupassen. Für uns ist es also selbstverständlich, dass wir Baupläne zur freien Verfügung stellen, wenn wir etwas entwickeln.
Im Falle von Laser4DIY, also im Bereich Laserstrukturierung, gibt es noch andere Gründe. Erst mal ist das, was wir entwickeln, kein neues Verfahren. Solche Maschinen gibt es im Industiebereich. Aber sie sind sehr teuer und daher uninteressant für offene Werkstätten wie unsere. Unser Ziel war es also, das Ergebnis möglichst kostengünstig zu halten. Open Hardware kann dabei helfen und war daher das Mittel unserer Wahl.
Seid ihr auf besondere Probleme gestoßen, weil ihr euer Produkt Open Source gestaltet habt?
In unserem Fall gibt es hauptsächlich Vorteile, einen Open-Source-Ansatz zu verfolgen. Eine Herausforderung war es, den Aufbau günstig zu halten, insbesondere bei der Konstruktion der Laserquelle. Denn die muss genug Leistung haben, um das Kupfer abzutragen. Wir haben sie daher selbst entwickelt, weil konventionelle Laserquellen sehr teuer sind. Dazu mussten wir viel experimentieren. An dieser Stelle ist der Open-Source-Ansatz gut geeignet, da uns jetzt andere bei der Verbesserung niederschwellig helfen können: indem sie sich die Dokumentation anschauen und uns Feedback geben. Außerdem können sie die Laserquelle für andere Anwendungen nutzen. Darin liegen die Vorteile von Open Source. Das wäre mit einem geschlossenen Ansatz nicht möglich.
Ihr seid schon sehr weit mit eurem Projekt: Wie können sich andere beteiligen?
Wir haben einen Prototypen gebaut, der funktioniert. Natürlich gibt es noch Baustellen und Verbesserungsbedarf. Durch die Unterstützung des Prototye Fund Hardware sind wir jetzt in einer Betatestphase. In dem Kontext schreiben und verbessern wir die Dokumentation. Dabei helfen uns verschiedene Betatester, indem sie uns Feedback geben, während sie das Gerät nachbauen. Wenn wir damit fertig sind, gibt es die Dokumentation und andere können es nachbauen. Erfahrungen, die dabei entstehen, interessieren uns natürlich auch. Besonders helfen uns Expert*innen für Laserquellen, die uns z.B. bei der Leistungssteigerung des Lasers helfen können. Wenn wir es schaffen, hier eine gute Basistechnologie zu entwicklen, können wir die in vielen anderen Maschinen nutzen, wie auch in klassischen Laserschneidern. Darüber hinaus freuen wir uns natürlich über jeden und jede, der oder die sich für das Projekt interessiert.
Gibt es Zukunftspläne?
Wir wollen das Gerät nicht selbst produzieren und vertreiben, werden aber wahrscheinlich einen Bausatz anbieten. Allerdings müssen wir vorher deutlich mehr Praxiserfahrung sammeln. Bisher haben wir uns hauptsächlich mit der Entwicklung beschäftigt und nicht so sehr mit der Anwendung.
Desweiteren gibt es noch viel Potenzial für Weiterentwicklungen. Denn das Platinendesign bzw. die Erstellung der Leiterbahnen ist nur der erste Schritt bei der Herstellung einer Platine. Es gibt noch viele andere wichtige Aspekte, wie das Bohren von Löchern oder Erstellen von Durchkontaktierungen. Oder auch das präzise Aufbringen von Lötstopplack. Daran werden wir arbeiten.
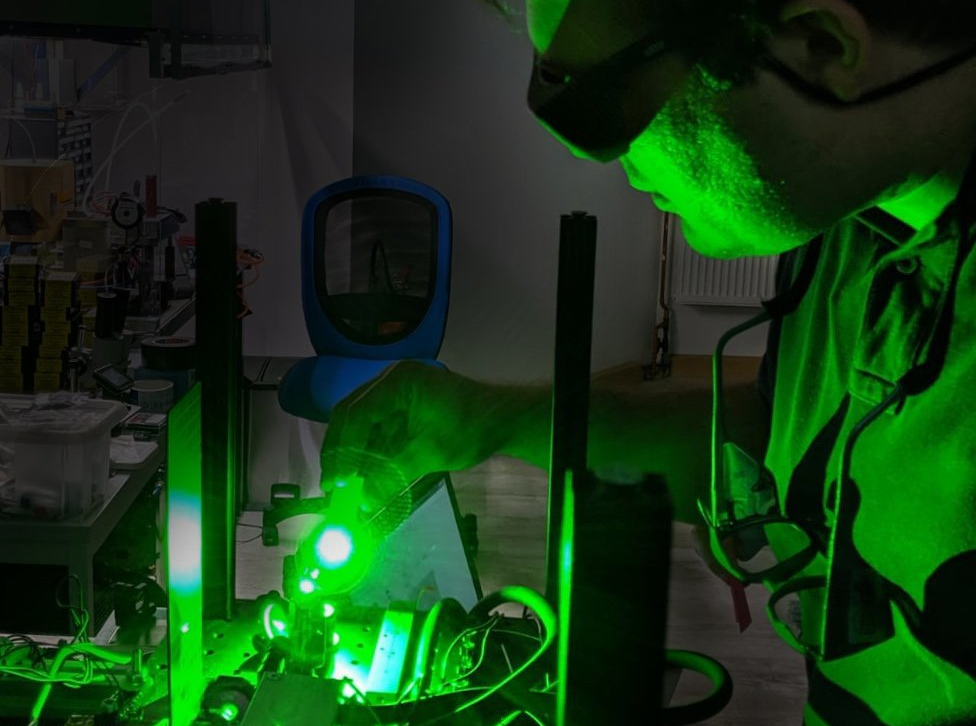